Innovating with purpose, delivering with care
In our PrimeChain products, industrial operations, and development, PRIME utilizes the Fishbone framework to emphasize the interconnectedness of the four key factors (Men, Material, Machine, and Method) which play a critical role in ensuring efficient and reliable product performance and services at PRIME. We learn, grow, and build future success through years of experience.
We pride ourselves as your reliable partner in the chain conveyor industry!
OUR EXPERTISE
Comprehensive conveyor solutions
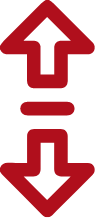
Vertical Conveyors

Horizontal Conveyors
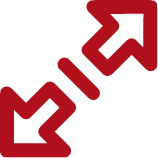
Inclined Conveyors
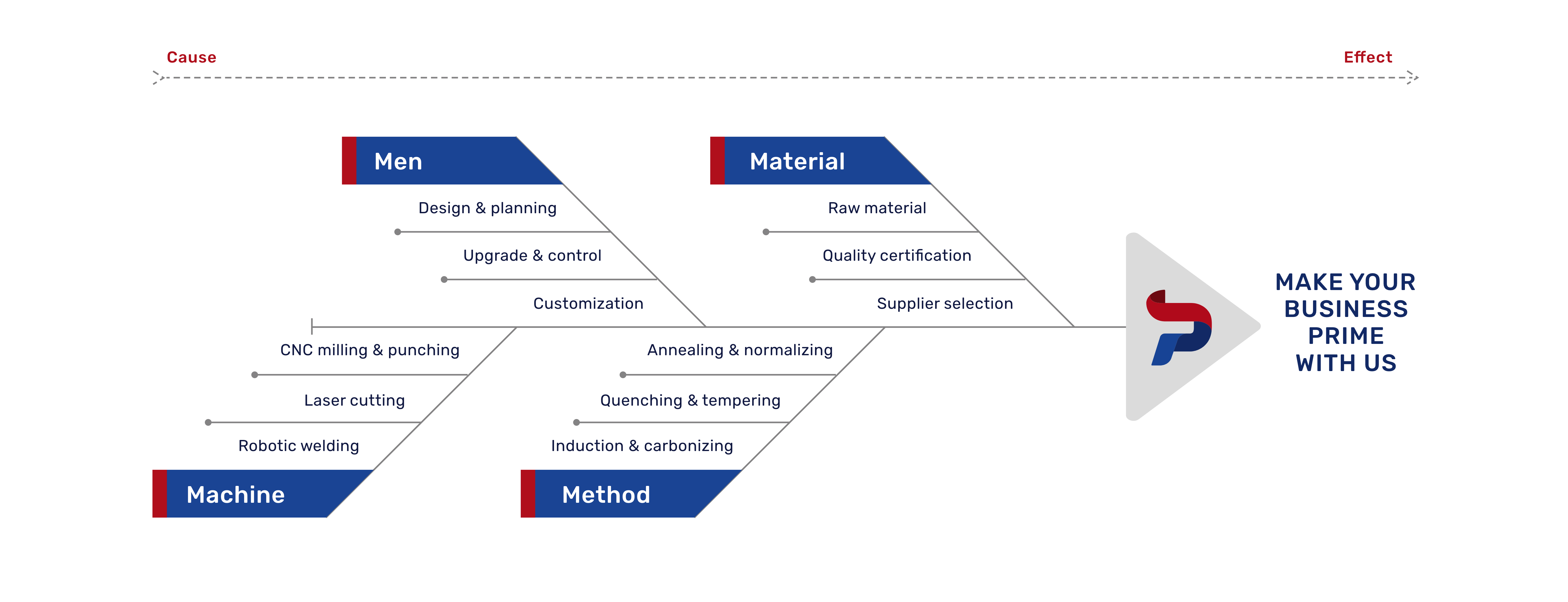
OUR STRENGTH
Men
“Engineers are the architects of progress, designing solutions that drive industries forward.”

Design & planning
Crafting PrimeChain products tailored to operational requirements. Our engineers work closely with clients to develop innovative designs that enhance efficiency and address specific needs. With meticulous planning, we ensure every detail is considered to optimize performance and minimize downtime.
Upgrade & control
Enhancing existing systems through comprehensive upgrades. Our team ensures that outdated systems are transformed to meet modern standards, incorporating advanced technologies and controls for seamless operation. This includes integrating smart solutions for monitoring and maintenance.
Customization
Delivering solutions that meet unique industry demands. From specialized layouts to custom-built components, our engineers have the expertise to create systems that align perfectly with your operational goals, ensuring maximum adaptability and functionality.
OUR STRENGTH
Material
“The strength of any structure lies in how the solid foundations made for enduring success.”
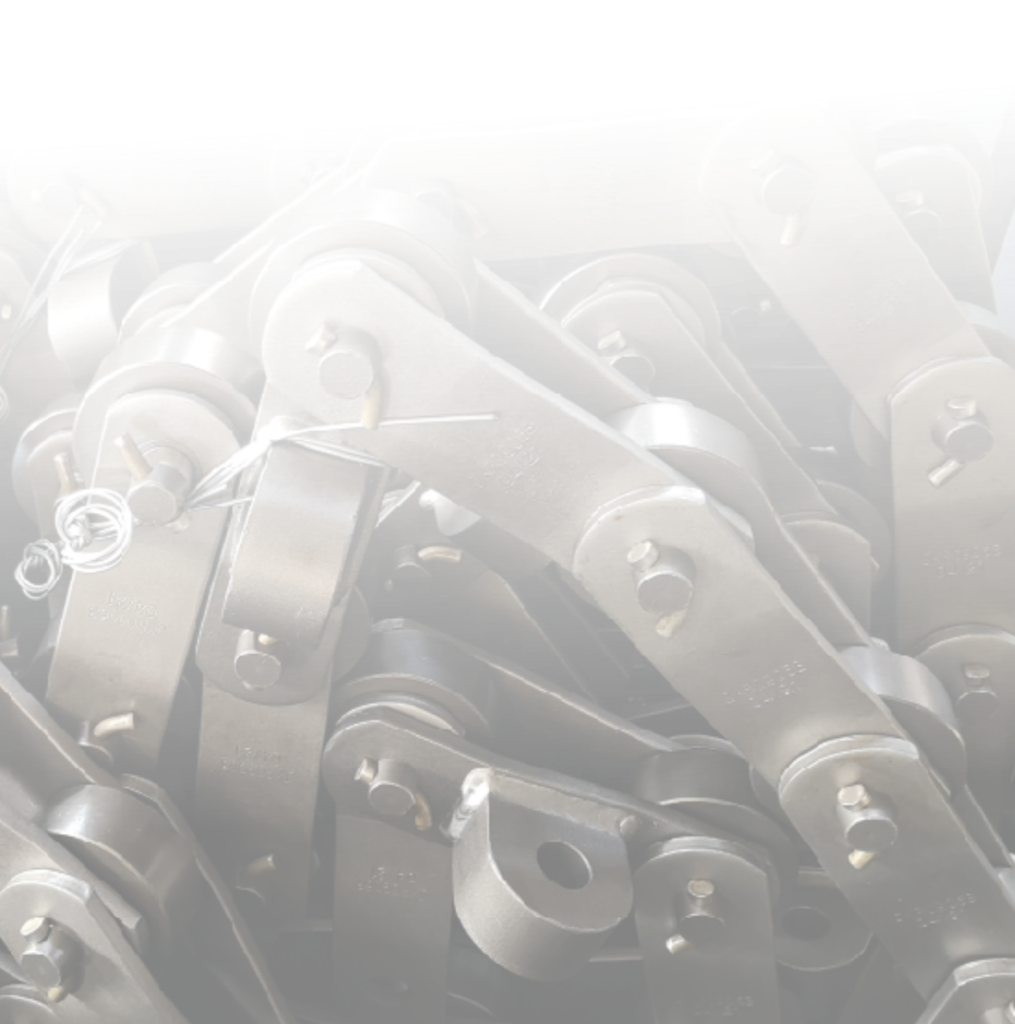
Raw material
We partner with trusted suppliers who meet our stringent quality criteria. This ensures that every component used in our PrimeChain conveyor systems is built to last and performs at peak efficiency under demanding conditions.
Quality certification
Every material we use is backed by certifications verifying its compliance with industry standards. From tensile strength to chemical composition, we ensure that our materials meet all required specifications.
Supplier selection
Advanced testing methods, such as spectral analysis and metallographic evaluation, allow us to confirm the material properties. This guarantees the robustness and reliability of our systems across various applications.
OUR STRENGTH
Machine
“With precision, we shape potential, turning each movement into a catalyst for your success.”
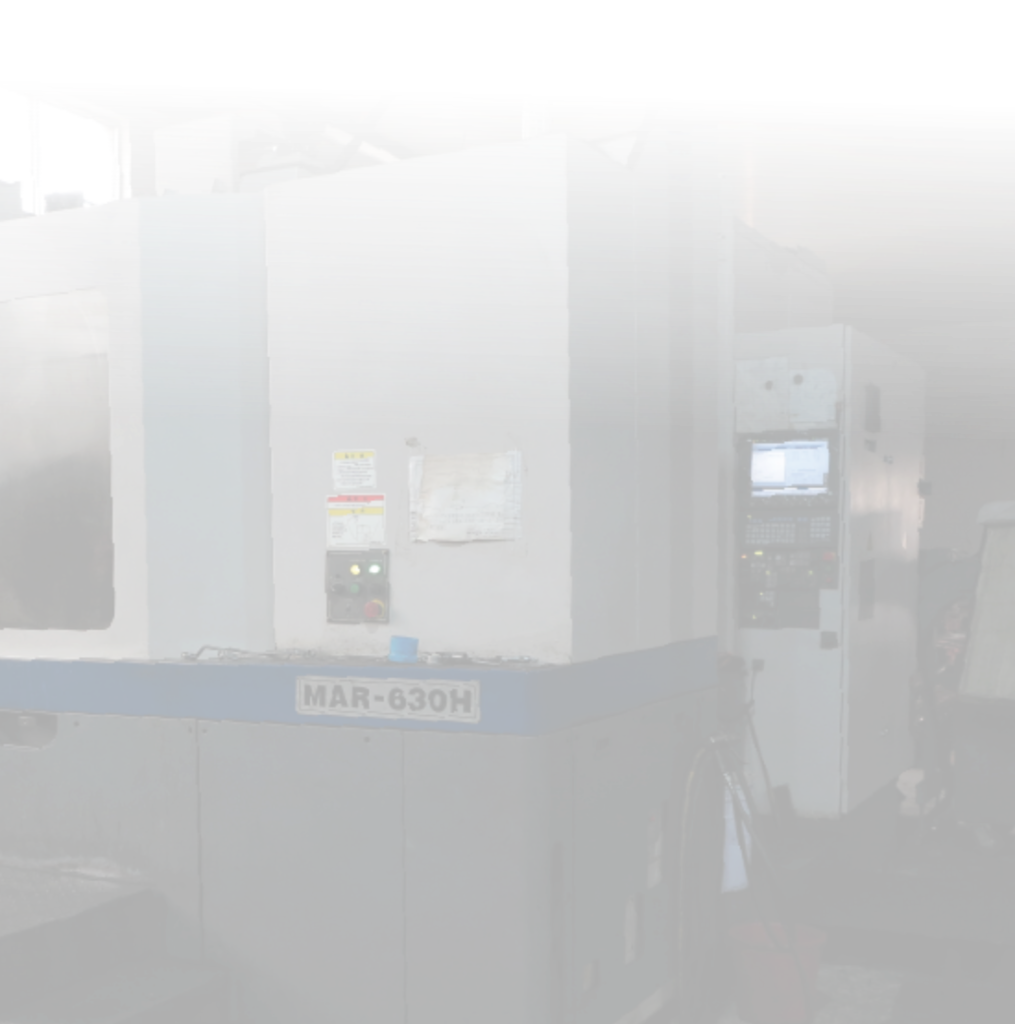
CNC milling & punching
Our CNC milling and punching machines allows for precise shaping, drilling, and contouring of components. These machines are designed for high-speed, high-precision operations, ensuring parts are formed to exact specifications for seamless integration into your chain conveyor systems.
Laser cutting
We use a high-powered laser machinery to cut materials with extreme precision. This process involves focusing, melting or vaporizing it to create clean, intricate cuts. Laser cutting provides superior accuracy and is ideal for complex designs, minimal material wastage, and smooth edges.
Robotic welding
Robotic welding utilizes automated welding robots equipped with sensors and programmable instructions to perform consistent, high-quality welds. Robotic welding ensures precision, repeatability, and faster production speeds while maintaining structural integrity and reducing human error.
OUR STRENGTH
Method
“Our well-defined processes ensure that every step we take brings us closer to delivering excellence.”
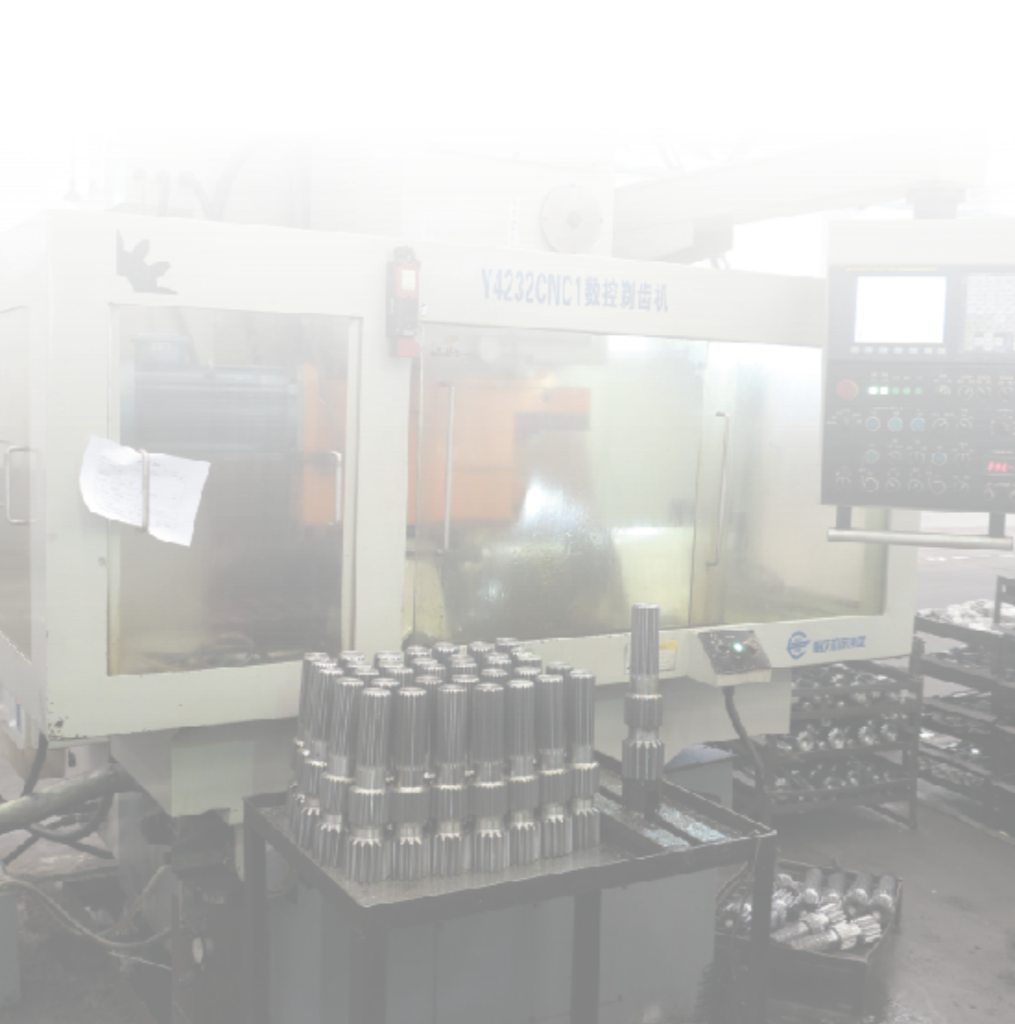
Annealing
This enhances the material’s ductility. which is vital for further shaping and forming, ensuring that the components maintain their structural integrity.
Quenching
This process is critical in industries like steel manufacturing where controlled cooling is required to improve material toughness, reduce residual stresses, and prepare material for further processing.
Induction
This process makes the material more resistant to abrasion while keeping the underlying material tough and ductile. Induction hardening improves service life and reliability under heavy loads.
Normalizing
This step is particularly important, ensuring the material can withstand the mechanical stresses they encounter in demanding environments.
Tempering
Tempering involves rapidly cooling the heated metal, to lock in hardness. This process helps achieve the desired mechanical properties, making the material resistant to wear.
Carbonizing
Carbonitriding and carbonizing are processes that increase hardness and wear resistance. Carbonitriding is typically used to improve surface hardness while maintaining a tough core.
OUR STRENGTH
Services
“Before the sale, we provide clarity. After the sale, we deliver confidence. Together, it’s a promise of excellence.”
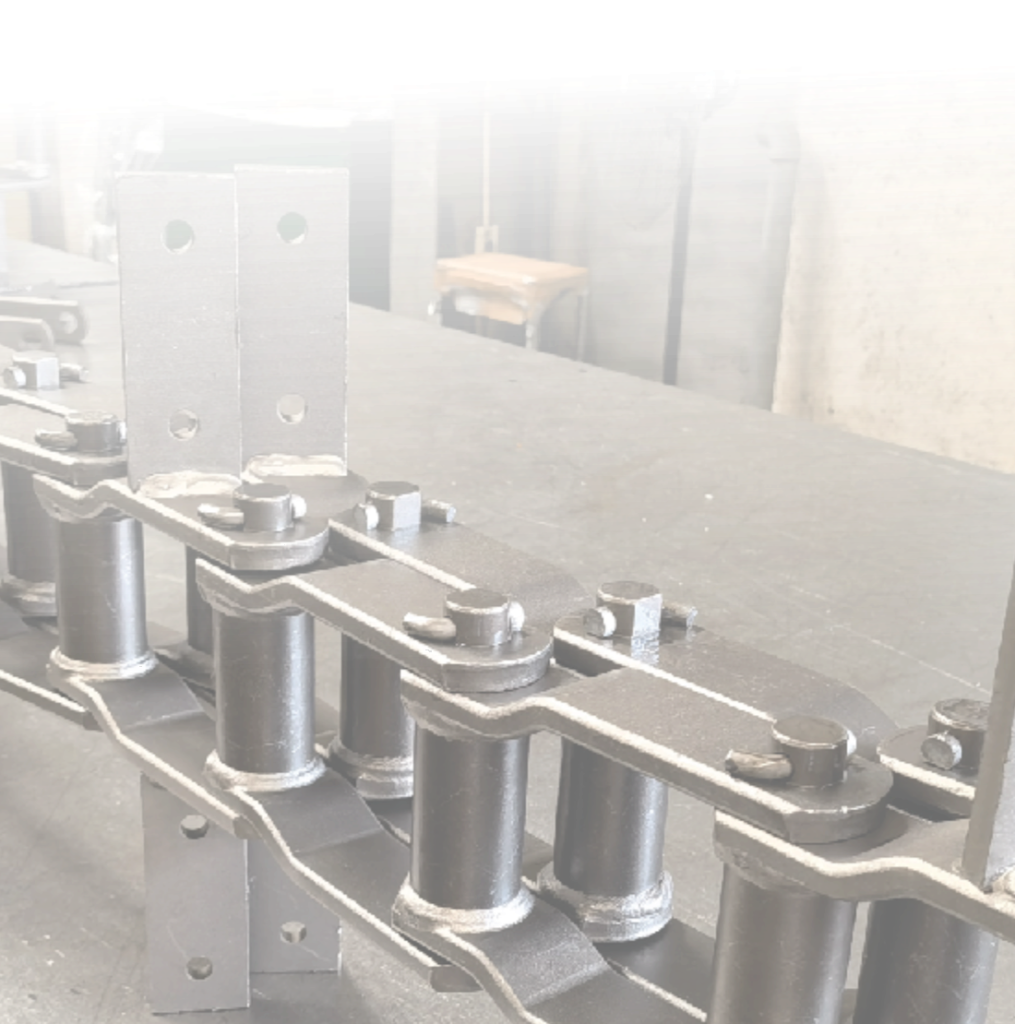
Before sales service
- Sample Checking
- Material Identifying
- Tensile Strength Testing
- Specific Measurements
- Inspection Reports
After sales service
- Installation Supervision
- Commissioning
- Periodic Checks
- Elongation Measurements
- Test Reports